|
Quick And Direct Information |
|
|
|
|
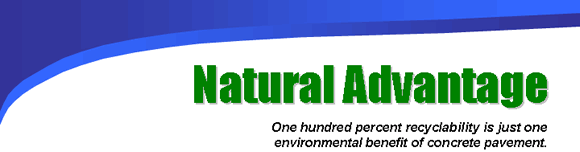
All pavements eventually have to be replaced, but did you know that at the end of their life, concrete pavements can be crushed and re-used?
Typically, the recycled material is used as granular fill, base course for new pavement, or as aggregate to strengthen new concrete pavement.
State and local agencies have specified recycled aggregate for all types of concrete pavements. In fact, some state departments of transportation allow up to 100% of recycled concrete aggregate in concrete mixtures.
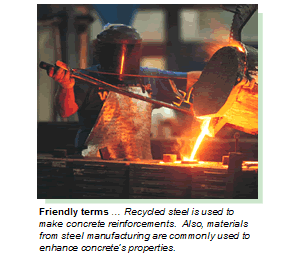

Concrete is an almost inert material. Because of its inert nature, but also because it cures to a solid form, it is ideal for using industrial by-products that otherwise would have been deposited in landfills.
Many of these materials actually enhance the properties of concrete pavement!
Reusing these materials also lightens the load on our landfills. Examples of these materials include industrial co-generated materials such as fly-ash (from power generation industry) and blast furnace slag (from steel manufacturing).
Aggregate, for example, can contain blast furnace slag. It is not uncommon to replace 20-50% of the cement with either fly ash or blast furnace slag.
Another added benefit of using these materials in concrete pavement is the reduction of CO2 emissions associated with concrete production.
Yet another product commonly recycled and reused in concrete is steel. Reinforcing steel used in concrete pavement is often made from recycled steel.
And like concrete itself, old rebar is recycled into new. Incidentally, did you know that steel and concrete are among the most recycled materials in the world? The asphalt industry would have you believe asphalt is the most recycled material in the world, but the truth is that much of that recycling happens because asphalt pavements require complete demolition and reconstruction every 8-10 years. In sharp contrast, a comparable concrete pavement can easily last up to 40 years.

By eliminating the cost of removing old concrete and factoring in savings on disposal costs, potential use of recycled materials, and potential road damage from transport of virgin or waste materials, some states have estimated savings of up to 50% to 60% savings from using recycled aggregates versus buying new aggregate.
In-place recycling techniques have the potential for saving even more money. Using an in-place system also saves on wear and tear of highways and roads, saves fuel, and improves air quality by reducing exhaust fumes.
Recycling concrete is a smart and environmentally-conscious choice that saves resources. With in-place recycling, the recycling process has become even more cost-effective, too!
In-place concrete recycling reduces construction costs because a contractor doesn’t have to locate a recycling center or pay for trucking the materials away. This saves money for taxpayers and agencies.
Printer-Friendly Information: |
|